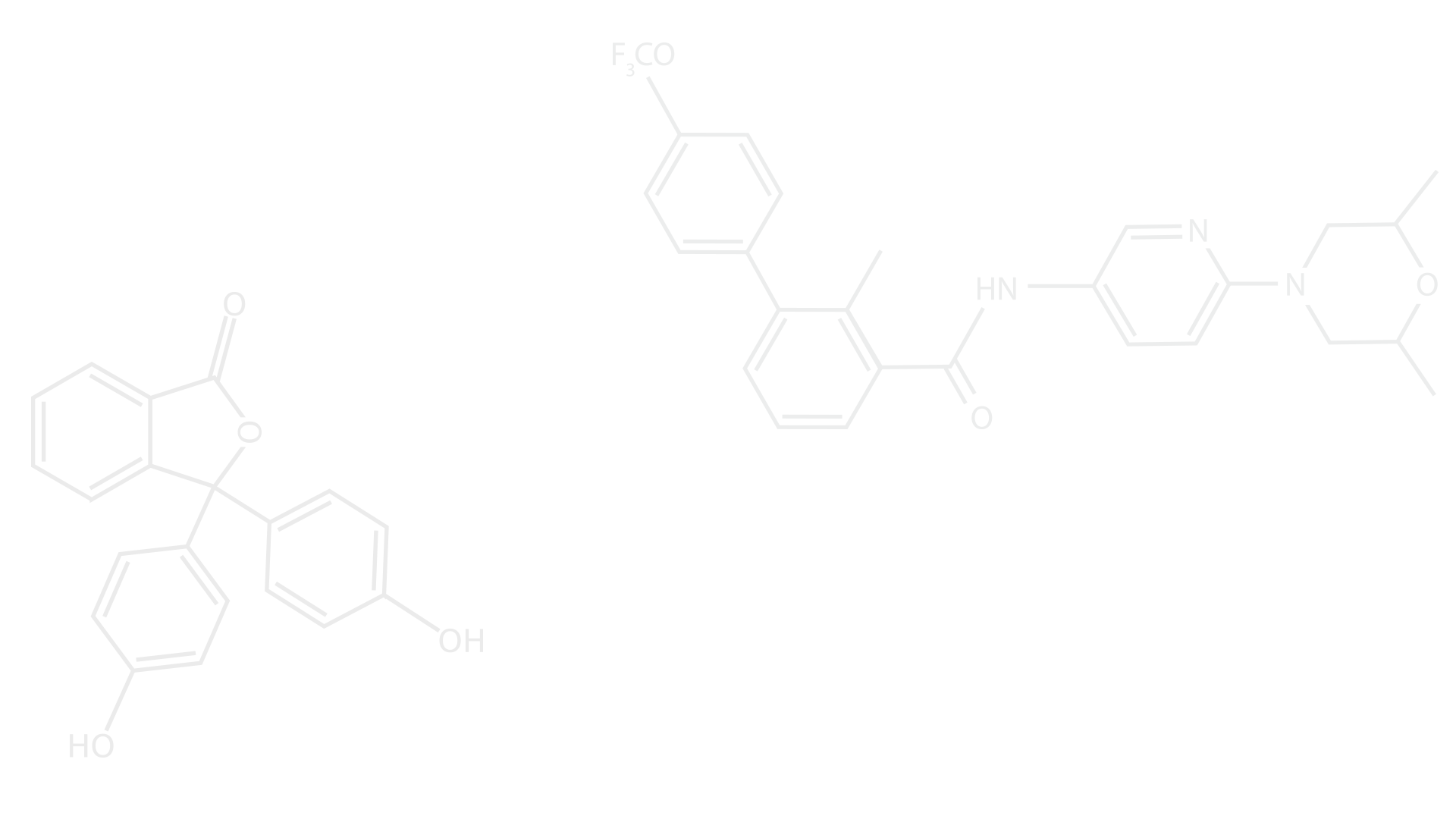
Pentathlon Robot
Abstract
Analysis
Construction
Results
The ASME 2017 Design Challenge is modeled after the 2016 Rio Olympics. Participants must build a robot to compete in Olympic style events. These Olympic events include a 10 meter sprint, golf ball hit, tennis ball throw, weight lift and stair climb. The sprint and stair climb event success is measured by time elapsed to complete the event. The weight lift is measured in weight lifted multiplied by height lifted, Newton-meters. The golf ball hit and tennis ball throw are evaluated by distance from robot. A robot was designed to meet this criteria. The design used analysis methods of statics, dynamics, and machine design to create the basis of minimum performance standards for each mechanical system. The robot was built primarily of VEX Robotics parts, and of 3D printed custom designed parts. Mechanical systems are also required to have a failsafe position to ensure safety of robot drivers and spectators. During construction of the robot, several design changes were made to accommodate space allowances and clearance issues between mechanical systems. The robot was tested at the ASME Student Design Expo at Central Washington University, where it competed against robots made by other university participants. The robot is considered successful as it falls within 10% of the expected performance parameters for each event.
The design consists of 4 different systems to achieve the 5 separate tasks and 2. The process of analysis was based on first finding limiting design factor and free design factors. After finding the design factors, each system was analyzed to find the required power, stress analysis and weight parameters as well as expected performance. The 3D printed parts were optimized for conserving weight while meeting the required dimensions. The claw was first analyzed to find the minimum dimensions of the support base for the weight lifting event. After finding minimum dimensions, a safety factor of 2 was applied, and the design was analyzed using finite element analysis to confirm stress concentration areas.
The device was built from the drive base up, followed by the elevator, arm and kicking mechanism. Major manufacturing issues arose from initial design interference between electrical systems and fasteners. The drive base wheels were found to be too heavy for the elevator motors, so smaller diameter wheels were mounted. The change in wheel diameter required the 3D printed kicker to be shortened for ground clearance during the kick.
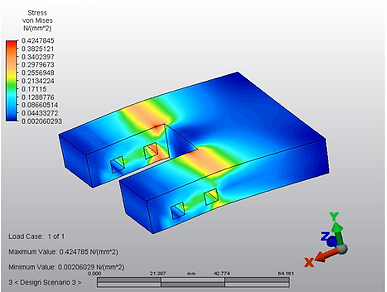
The resources required to test the robot include an operator and a judge. The operator performs each test while the judge records the time and distance measured. Video recordings can be used to verify timed test results, and photo evidence can be used to measure distance travelled. Preliminary data recording is performed on paper, and the robot designer to analyze design issues during each event performs any further analysis. Each event is timed, and results are analyzed on the test site. Typically, each test requires one button push, so the judge and operator can be the one in the same. The accuracy of distance measured events is dependent upon the measuring tape used. The majority of the tests used an English measuring tape, so all distances were converted to metric units. Conversion introduces error, however, each event is to the nearest 10th of a meter, and nearest .1 second. All data is recorded on paper, then input to digital storage for statistical analysis. Data shall be plotted to show data spread and performance error.
Testing
The Throw
The primary issue during testing was the geometry of the claw mechanism. The first test was unsuccessful as the motor threw the claw and the tennis ball during the event. The arm was then redesigned.
The Hit
The first tests of the hit was had a reliability of 1.016, however only reached half the required 2.5 meters. The maximum distance travelled was 1.87 meters.
The Lift
The arm was determined not to have the appropriate power to lift 2kg, in the configuration required to perform the tennis ball throw. When tested at 2kg, 1 kg, and .5kg, the arm was not able to move a measurable distance. The arm successfully lifted .25 kg to the height of the arm.
The Sprint
The first tests peformed found that during major drive base use, the robot would disconnect from the controller via VEXNet. After speaking several VEX alumni, it was determined that the electrical layout of the motors on the VEX Cortex throw the fuse, as all motors are on the same fuse. To remedy this electrical issue, motors should be split between the two fuses on the Cortex and the program should reflect the changes.
The final results of the Sprint showed the robot completing 10 meters in 35 seconds.
​
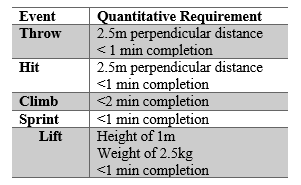

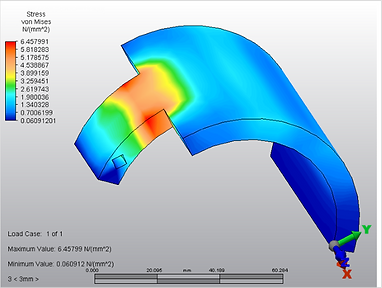

My Channel
My Channel

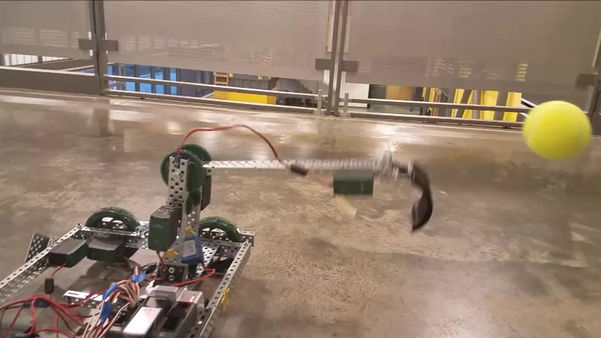